Support & MaintenanceHandling of Chains and Sprockets
Roller Chains/Sprockets for Roller Chain
Lubrication (Oiling)
Lubrication is extremely important for roller chain transmission. Improper lubrication could shorten the service life of a roller chain. Lubrication for roller chain transmission is also extremely important because chains have recently been used under more severe conditions such as high speeds and heavy loads.
The following is a list of lubrication points, lubrication methods, and types of lubricants, so be sure to lubricate chains with reference to this list.
Lubrication points
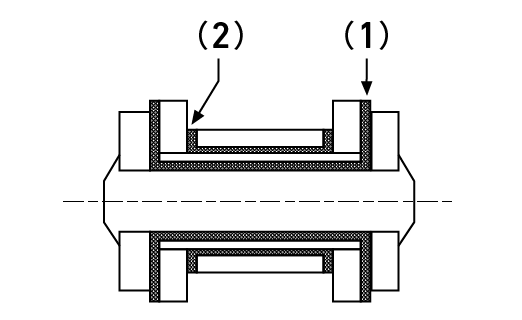
The important lubrication points for roller chain lubrication are (1) and (2) in the figure.
- Lubrication between pins and bushings
This prevents wear between the pin and the bushing, which is the main cause of wear on the roller chain. - Lubrication between bushings and rollers
This prevents wear between the bushing and roller, reduces noise, and absorbs impact loads.
Lubricating oil
In general, use a high-grade industrial lubricant. Select a lubricant with appropriate viscosity according to the ambient temperature, lubrication type, and chain size from the table below.
Lubrication type | I, II | III | |||||||
---|---|---|---|---|---|---|---|---|---|
Ambient temperature (°C) | -10~0 | 0~40 | 40~50 | 50~60 | -10~0 | 0~40 | 40~50 | 50~60 | |
Chain number | 50 or less | SAE10W | SAE20 | SAE30 | SAE40 | SAE10W | SAE20 | SAE30 | SAE40 |
60・80 | SAE20 | SAE30 | SAE40 | SAE50 | |||||
100 | SAE20 | SAE30 | SAE40 | SAE50 | 120 or more | SAE30 | SAE40 | SAE50 |
Caution
- Do not use waste oil as it may contain foreign matter, dust, or chips, or heavy oil or grease as they have a high viscosity and cannot penetrate the area between the pin and the bushing smoothly.
- If the ambient temperature is below -10°C or above 60°C, a special lubricant is required. In such cases, please contact us.
Commercial lubricating Oil (for reference)
ManufactureViscosity | Idemitsu Kosan Co., Ltd. | ENEOS Corporation | ||
---|---|---|---|---|
SAE10W | Daphne Mechanic Oil | 32 | FBK OIL RO | 32 |
SAE20 | 68 | 68 | ||
SAE30 | 100 | 100 | ||
SAE40 | 150 | 150 | ||
SAE50 | 220 | 220 |
*Manufacturers’ names are listed in no particular order.
Type | Lubrication method | How to perform lubrication | Illustration | |
---|---|---|---|---|
I | a | Brush or oil bottle method | A method of lubrication with a brush or oilcan periodically (every 8 hours), depending on usage conditions | ![]() |
b | Drip lubrication | A method of lubricating a chain by applying about 20 drops of oil per minute | ![]() |
|
II | Disk lubrication | A method of applying oil with a disc attached to the sprocket shaft | ![]() |
|
Oil tank lubrication | A method of pouring oil into a sealed casing and immersing a part of a chain in the oil | ![]() |
||
III | Forced lubrication | A method of forced injection lubrication using a casing that does not leak oil and circulating the oil by means of a pump | ![]() |
Maintenance/Inspection
Maintenance
(1) Caution during installation
- Chain elongation is caused by the wear between the pin and the bushing.
- Each chain is coated with anti-rust lubricant at the time of shipment. Do not wash or wipe off the lubricant when installing chains. Also, be careful not to place the chain directly on the floor to prevent sand or dust from adhering to it.
(2) Timing of replacement
- When the chain elongation reaches +1.5%. (When the number of teeth is 60 or more, the allowable elongation becomes smaller as shown in the graph below.)
- When the link plate is significantly damaged, cracked, or deformed.
- When the chain is found to have significant scratches, cracks, or rotation defects.
- When a bent pin or warped link plate is observed.
- Significant rusting and chain bending defects are observed.
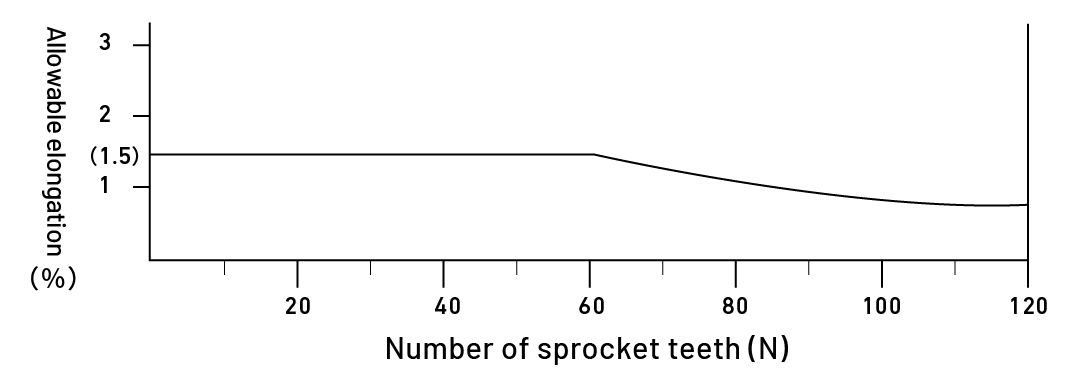
Caution
- When replacing a chain, avoid replacing only one part of the chain with a new one. When replacing a chain, replace the entire chain with a new one.
(3) Check Oil Lubrication
- Remove the chain periodically and clean it with kerosene. After that, fully lubricate the chain.
Caution
- When cleaning, do not use acid, alkali, gasoline, or benzine.
- Powders and foreign matter that accelerate wear must be completely removed.
- Metal surfaces cleaned with solvents are prone to rusting, and should be lubricated immediately to prevent rusting.
- Inspect the contact surfaces of the pins and the bushings, and if they are shiny, this indicates that the lubrication was proper. Apply oil again and use the chain.
(4) Chain elongation measurement procedure (caliper measurement)
- Chain length is usually measured by applying a load of approximately 1% of the average tensile strength. To measure an existing chain, measure the inner and outer dimensions between the rollers on the tension side as shown in the figure below.
- To minimize measurement error, measure at least 6 links.
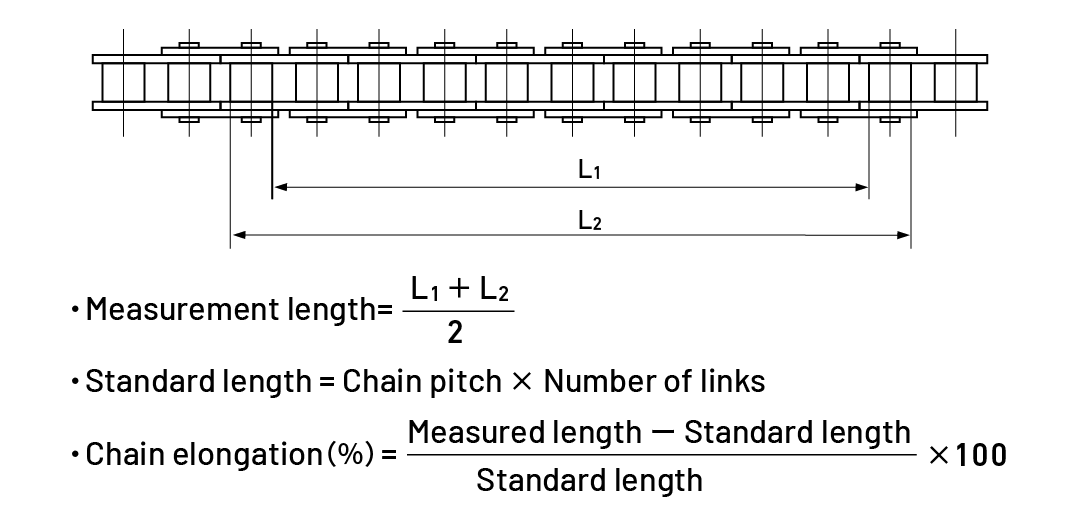
(5) Chain elongation measurement procedure (measurement with a measuring tape)
- To avoid measurement error, remove the chain and measure a distance close to the number of all links in a straight line.
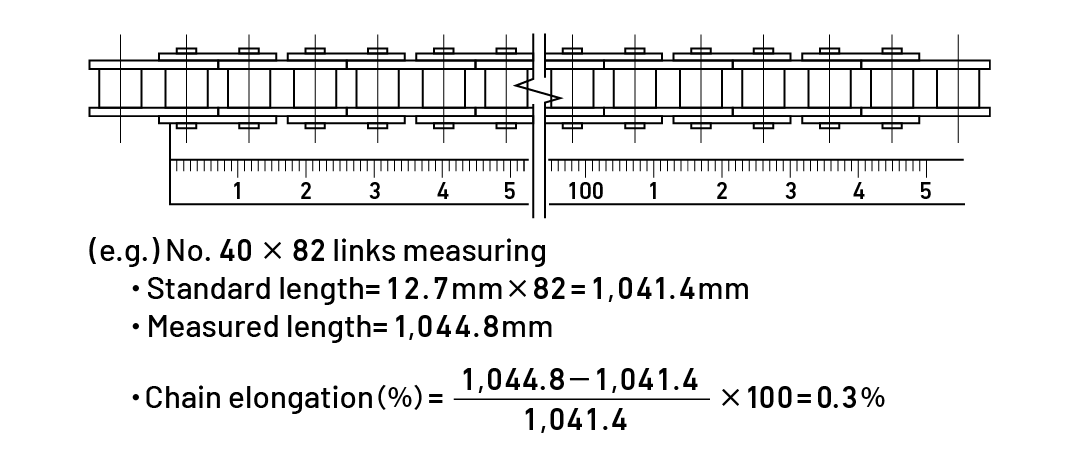
Inspection
When roller chains and sprockets are installed, perform the trial run inspection shown below before operation. In addition, since conditions may change over time during operation, perform daily and regular inspections to ensure safe use.
(1) Trial Run Inspection
- Check the chain is correctly installed
- Check the clips, split pins, etc. at the chain joint are correctly installed
- Check the split pins at the chain joint are correctly spread
- Check the appropriate take-up tension (Not too loose or too tight)。
- Check that the chain doesn’t touch chain cover
- Check that chain is lubricated properly
(2) Daily Inspection
- Check for abnormal vibrations, noises, etc.
- Check obstacles that may interfere with the chain and sprocket
- Check the chain components, dirt, corrosion, improper lubrication etc.
- Check each components for scratches, deformation, damage or other abnormalities.
- Check the roller rotation, bending, or gaps in each part
- Check the condition of the contact area with the sprocket
- Check the chain wear elongation
- Check abnormality of the joints, clips, or split pins
- Check rusting of the chain (Red rust due to poor lubrication or rust due to environmental deterioration)
- Check lubricating oil carbonization or other deterioration
- Check adhesive powder or forging matter that accelerates wear
(3) Periodic Inspection
- Check the paragraphs (1) and (2) above visually or with a measuring device while the machine is running, stopped, and with the chain removed.
- Perform regular inspections according to the usage conditions and environment. If the usage conditions are severe, increase the number of inspections.
(4) Other
- Predict failures are take measures to prevent accident according to the inspection result.
Clarification of problems and Countermeasures
Problem | Probable Causes | Countermeasures |
---|---|---|
Wear of parts![]() |
|
|
Pin rotation![]() |
|
|
Abnormal noise |
|
|
Chain vibration |
|
|
Wear of the inner plate and side of the sprocket teeth |
|
|
Poor chain bending |
|
|
Chain rides up on sprocket teeth |
|
|
Chain doesn’t come off from sprocket smoothly |
|
|
Broken pins![]() |
|
|
Broken pins![]() |
|
|
Broken offset pin![]() |
|
|
Fatigue failure of a plate![]() |
|
|
Stress corrosion cracking of plates![]() |
|
|
Broken rollers![]() |
|
|
Worn plates![]() |
|
|
Fractured plate![]() |
|
|