Support & MaintenanceHandling of Chains and Sprockets
Conveyor Chains/Sprockets for Conveyor Chain
Lubrication (Oiling)
Lubrication is extremely important for conveyor chains. Improper lubrication could shorten the service life of a conveyor chain. Nowadays, standard conveyor chains are increasingly used in harsh conditions, making lubrication of chains more important than ever. Please note that depending on the usage environment, lubrication may not be possible. In such cases, please contact us.
The following is a list of lubrication points, lubrication methods, and types of lubricants, so be sure to lubricate chains with reference to this list.
Lubrication points
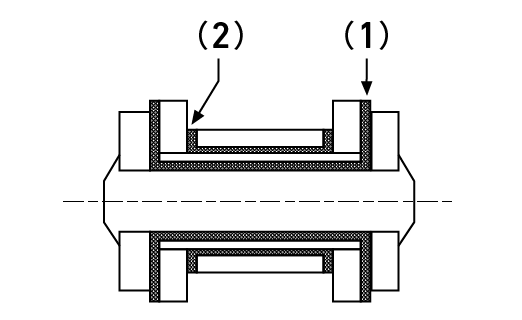
Lubricate the chain at the points (1) and (2) by dropper or brushing
Caution
- In the early stages of operation, the lubrication interval should be as short as possible to allow for initial wear of the sliding parts.
- Although rust-preventive oil is applied at the time of shipment from our factory, before starting actual operation, please be sure to thoroughly lubricate the product (grease) and operate it without load for 30 minutes or more. This no-load operation allows the lubricating oil to penetrate into each part, increasing its effectiveness.
Commercial lubricating Oil (for reference)
ManufactureViscosity | Idemitsu Kosan Co., Ltd. | ENEOS Corporation | |
---|---|---|---|
ISO VG | 150 | Daphne Super Gear Oil 150 | BONNOC AX150 |
220 | Daphne Super Gear Oil 220 | BONNOC AX220 |
*Manufacturers’ names are listed in no particular order.
Caution
- Special lubricating oil is required when the ambient temperature is below 0°C or above 50°C. Also, depending on the usage environment, lubrication may not be possible. In such cases, please contact us.
Maintenance/Inspection
Timing of replacement
When a chain is used, wear occurs in various parts, and the degree of wear can be used as a yardstick for the use limit of the chain.
(1) Link Plate Wear
The undersides of link plates are worn out due to the contact with the transported materials and the casing. Wear is also caused by contact between the inner and outer link plates, and the contact between the inner surface of the inner links and the side of the rollers.
Parts | Timing of replacement | Remarks |
---|---|---|
![]() |
t = 13T | When the chain is subjected to lateral loads. |
b = A2 | When the link is in contact with the guide rail |
(2) Pin and Bushing Wear
When the chain engages with the sprockets, it undergoes a bending motion. The frictional wear between the pin and the bushing that occurs at this time causes pitch elongation.
Parts | Timing of replacement for carburized materials | Timing of replacement for hardened and tempered materials | Notes |
---|---|---|---|
![]() |
bA = 0.975 | bA = 0.85 | Pin breakage may occur when the cross-sectional area is reduced by one-half. |
![]() |
When the amount of wear on the inner or outer diameter is 0.025b or more | t = (A-b) × 12 × 0.4 |
(3) Roller Wear
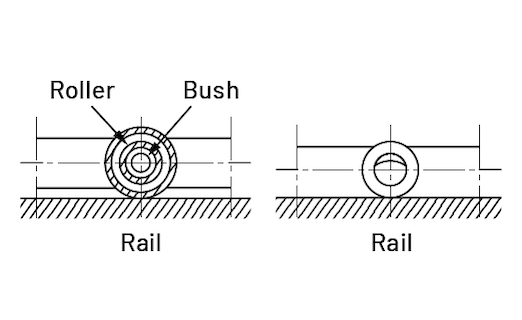
In the case of R-type rollers and F-type rollers, when the rollers wear out, the link plate touches the rail, increasing the abrasion resistance and chain tension. At that point, it is recommended to replace the rollers.
In the case of S-type rollers, you should replace the rollers with new ones when they are worn out and have holes or cracks in them.
(4) Chain Pitch Elongation
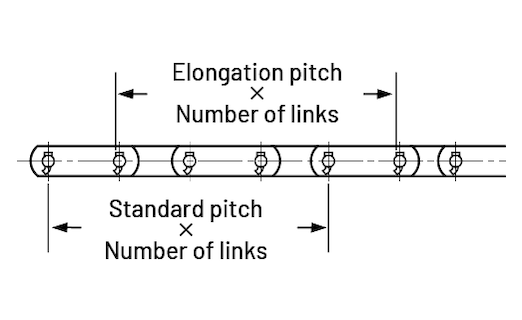
When a chain is used for an extended period, wear of the pins and the bushings causes the chain to elongate and ride on the sprockets, resulting in malfunctions. Therefore, the limit of pitch elongation should be 2 to 3% of the standard dimension. You should replace the chain with a new one when it reaches the limit.
Chain length should be measured with 4 or more links as shown in the figure.
(5) Sprocket Wear
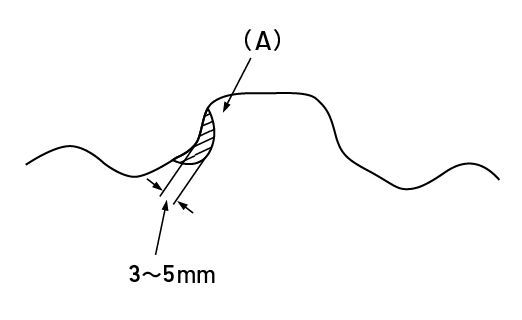
As sprocket wear progresses as shown in the figure, the rollers of the chain get caught on the tooth tips (A), causing the chain to become entangled (the chain becomes more difficult to separate from sprocket). The amount of wear on the bottom of the sprocket teeth varies depending on the size of the chain and the speed of the chain, but when 3 to 5 mm of the bottom of the sprocket teeth is worn, the sprocket should be replaced with a new one or repaired.
Inspection of Conveyor Chains and Sprockets
(1) Trial Run Inspection
- Check the chain and sprockets are correctly installed
- Check T-pins at the chain joint are correctly installed (Be careful of the bending angle)
- Check the appropriate take-up tension (Not too loose or too tight)
- Check there are no foreign matter interfering with the running of the chain
- Check that the chain is properly lubricated
- Check for abnormal sound (vibration or noise) during operation
(2) Daily Inspection
- Check for abnormal vibrations, noises, etc.
- Check for abnormal rust or dirt on the external part of the chain
- Check for abnormalities such as scratches, deformation, unevenness, or damage on the structural parts of the chain, especially on the link plate and roller
- Check the meshing by chain and sprockets, and chain can release smoothly
- Check the chain bending and smooth roller rotation。
- Check the chain wear elongation
- Check for unevenness in the contact area between the chain and the sprocket (inner surface of the inner plate, side of the sprocket)
- Check for the chain tension appropriately
- Check that the chain is properly lubricated
(3) Periodic Inspection
- Check the paragraphs (1) and (2) above visually or with a measuring device while the machine is running, stopped, and with the chain removed.
- Perform regular inspections according to the usage conditions and environment. If the usage conditions are severe, increase the number of inspections.
Clarification of problems and Countermeasures
Problem | Probable Causes | Countermeasures |
---|---|---|
General corrosion Corrosive wear |
|
|
Damage to pins, bushings, and rollers Deformation of the link plate hole |
|
|
Abnormal noise |
|
|
Chain vibration |
|
|
Side wear of the link plate and the sprocket |
|
|
Poor chain bending |
|
|
The chain rides up on sprockets. |
|
|
Chain separates poorly from the sprocket |
|
|